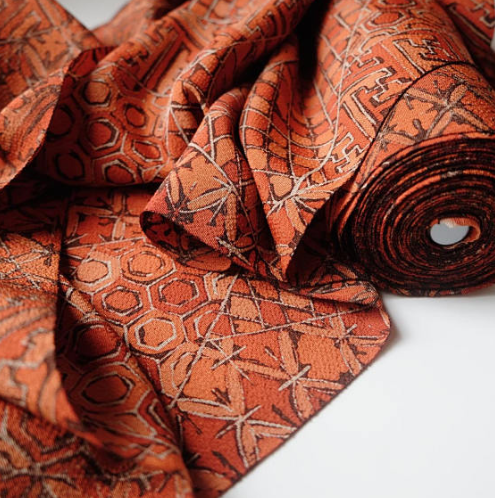
Silk Chirimen
Chirimen fabric is a silk crepe, the ultimate luxury fabric for kimono. It is a softly textured fabric made by the weft (crossways) threads being kept tighter than the warp (vertical) threads during the weaving process. Weft threads are twisted as they are woven, resulting in a crepe texture. Chirimen fabric drapes beautifully, and it is difficult to crease. It is a very old weaving style, and is typically dyed after weaving.
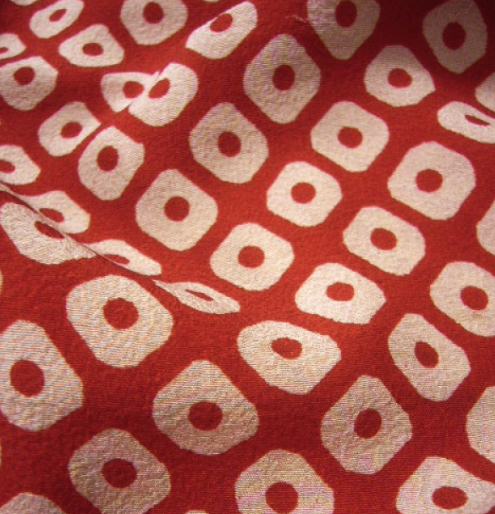
Kinsha
Kinsha is a type of chirimen, but is even finer and lighter crepe. Kinsha fabric is typically dyed after weaving using various dying and hand painting techniques. It has a smooth texture which results in crisp lines, perfect for painting or dying detailed scenes. Mon-kinsha is a Kinsha fabric with woven patterns.
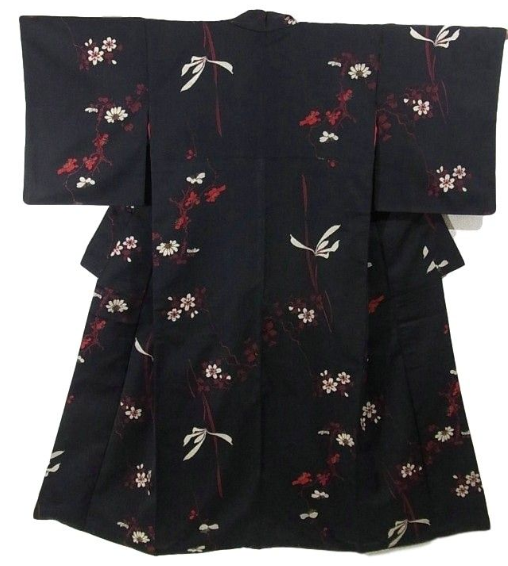
Omeshi
Omeshi fabric is also a crepe weave, but unlike with chirimen and kinsha, which are usually dyed after weaving, Omeshi threads are dyed before weaving and then the weaving creates the pattern. Omeshi are woven with strongly twisted pre-dyed threads and were often worn in the Imperial Court. This type of kimono was loved by Lenari Tokugawa (11th shogun).It is considered the highest rank quality among kimono silk textiles made with pre-dyed threads (Kasuri). The pattern is the same on both sides. A modern equivalent is jacquard weaving. Stripes are a common form of Omeshi patterning.
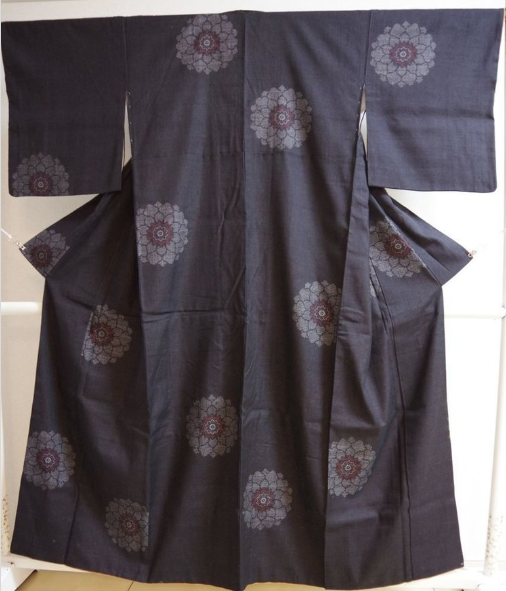
Tsumugi
Tsumugi kimonos are worn in Japan for casual visiting, informal events, classes and the like. The are prized for their patterning which is woven in, rather than dyed afterwards. Tsumugi fabric can be nubby and uneven in texture, appearing quite rustic due to the uneven thread widths. It often has the appearance of cotton, but usually feels softer, as it is often a blend of silk with cotton. Because the short threads are joined together so often, tsumugi fabric is time consuming to make.
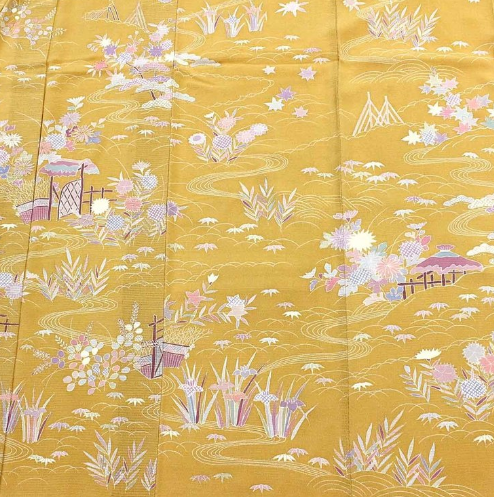
Ro Silk
Ro fabric is loosely woven from very fine silk threads, creating sheer, airy, summer kimono.
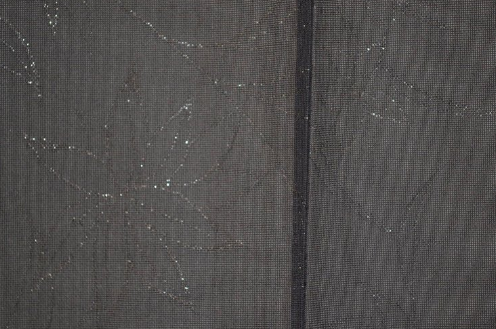
Sha Silk
Sha silk is a simple weave silk gauze, typically used for unlined summer kimonos. Sha fabric is much crisper than equally fine Ro silk. Different weaving techniques may be used to create a subtle pattern in the fabric, which is dyed or hand painted after weaving.
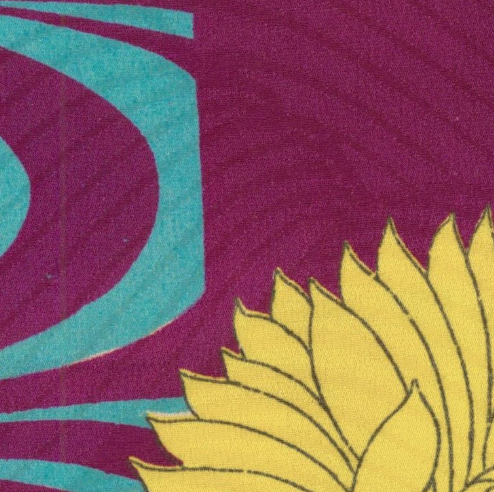
Rinzu Silk
Rinzu is a silk satin damask fabric. After the threads are initially died, they are woven to form a geometric or floral pattern, a shiny, subtle repeating pattern on a matte background. Two different types of silk threads may be used to achieve the pattern. Many Shibori techniques are done on rinzu silk, creating a complex, layering of pattern, color and shine. Rinzu is often used a base for shibori dying, adding another layer of depth and richness.
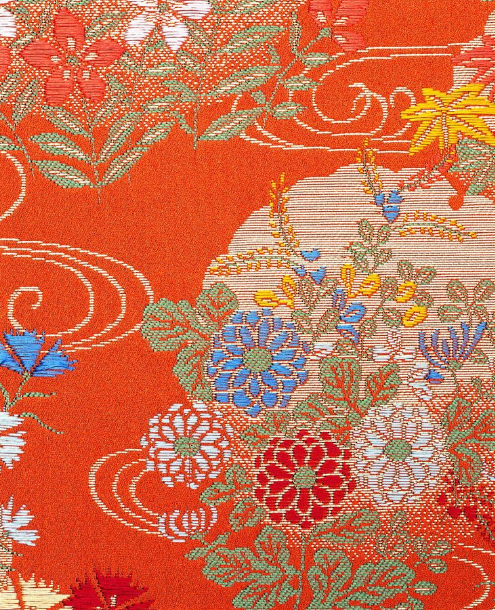
Nishijin-ori
Nishijin-ori is a textile produced in Kamigyo-ku, Kyoto. The name "Nishijin" (originally meaning "west position") came about because these gorgeous fabrics were produced in the area in Kyoto where the position of an army, then called "West Army" was in a civil war (O'nin no Ran) which ended in 1477. As it is woven by colorful threads, "Nishijin Ori" is gorgeous fabric, high quality, and can be stated one of key representatives of Japanese textiles.
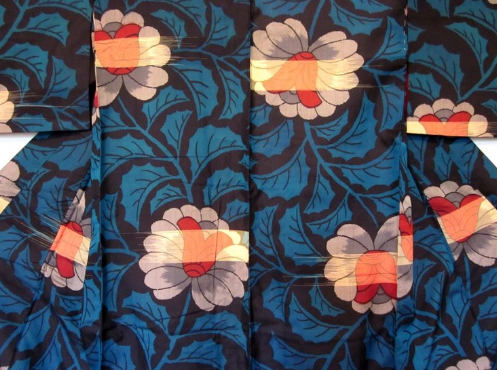
Kara-ori
Kara-ori is a technique of weaving textiles. The woven design of kara-ori stands out from the weft (horizontal stitch) and looks similar to embroidery, creating a luxurious fabric. Kara-ori kimono is known as one of the most gorgeous kimonos in the county and they are usually used for outfits in Noh plays.
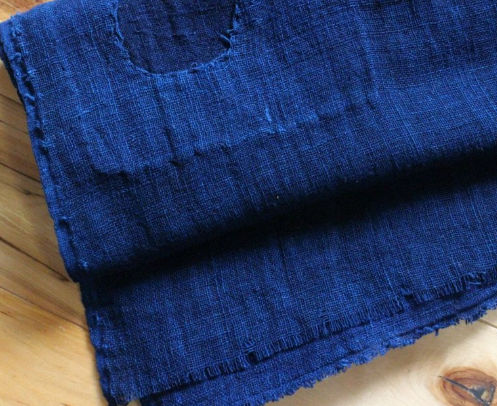
Hemp/Linen (Asa)
Fine handwoven linen or hemp bast fibers (the capillaries that raise water up into the plant) are used to make durable but light summer kimonos (jofu). Jofu fabric was originally worn by those in the samurai class.Threads were originally resist dyed in the tiniest motifs - sometimes called “mosquito” pattern before weaving by hand, but now, stencil dying may be used on the loosely woven fabric. This fabric is ideal for hot humid conditions and is comfortable to wear. Jofu kimonos are not worn at formal occasions, and the patterns are often based on blue (indigo dyes), or white color schemes.
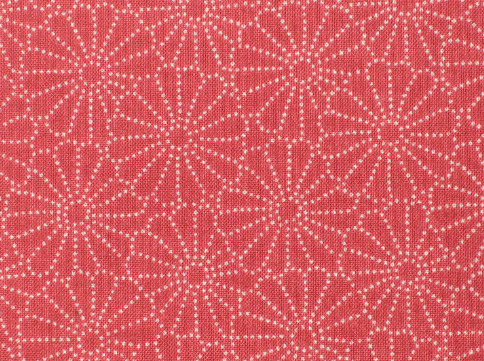
Cotton
In the 12-1400’s cotton began to replace hemp in workers’ clothing. Most cotton fabrics are plain weave and were commonly dyed with indigo, either as threads or as whole cloth. Threads were woven into stripes or plaids, or one of many kasuri patterns. Since indigo cannot be exposed to air until after it is in place on the fabric dip-dying into vats was the only option, and engendered the whole family of Shibori resist-dye techniques to create pattern.
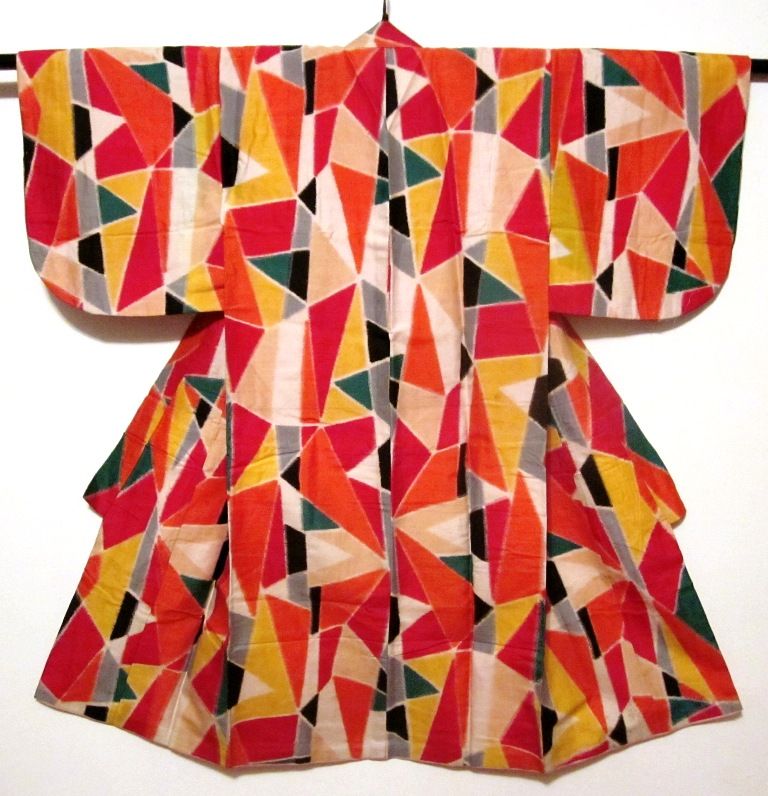
Meisen
Meisen style fabric was produced starting from the mid-1800’s through the first world war. Because of relative efficiency of these streamlined approaches to patterning resist areas, outlined above, these Meisen kimonos were much more affordable and were a major innovation sold in department stores in Japan.To make meisen fabric, threads are first loosely woven and then dyed using stencils. The lengthwise or the crosswise threads may be discarded at this point and new ones woven in to create the initial patterns. This is a flat, plain weave fabric. Meisen kimonos have a very modern feel in many cases, with the clear influence of the art deco and art nouveau designs that were popular at the time.
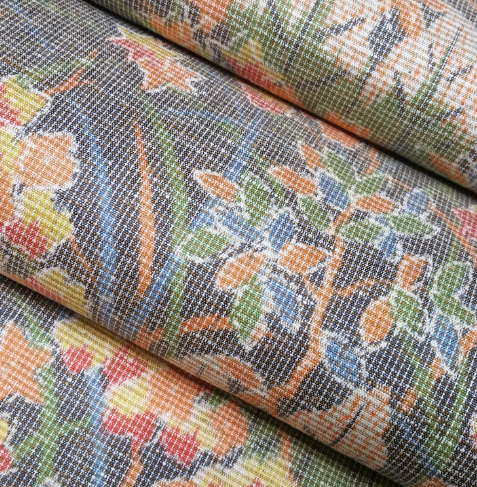
Ooshima Tsumig
Ooshima Tsumig is a plain weave silk, spun by hand, with very fine patterning by threads pre-dyed before weaving. The fabric is soft and difficult to wrinkle. Threads are dyed with plant dyes such as Japanese Hawthorn and Indigo with a technique specific to Oshima Tsumugi called “Ori Jime”. In another type of Oshima dying, Doro(mud) Oshima uses mineral rich mud and the subtle colors generated by the minerals and chemistry of the mud are considered particularly refined. Many repeated mud immersions dyings are required to build up depth of color which may be combined with many immersions in other natural dyes.
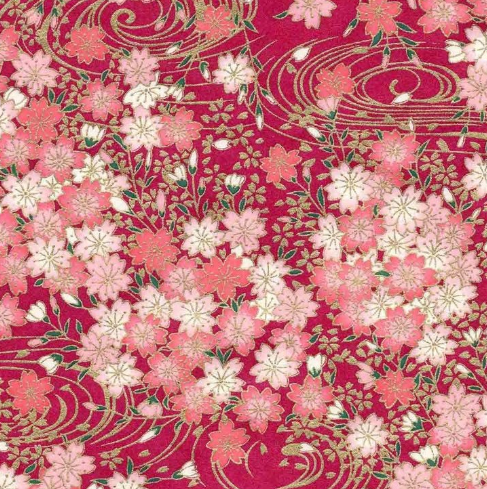
Yuzen
Yuzen, invented around 1700, is probably the most famous of Japanese dyeing techniques. It is produced by a combination of either freehand or stenciled paste-resist work and hand-application of dyes. With the cloth (either silk or cotton) stretched on a frame, a pattern is applied with a fine brush using a non-permanent blue vegetable dye, and then covered freehand with paste; or else the paste is applied directly with a stencil. A thin soybean extract is then brushed over the entire cloth. The cloth is then moistened with water, and dye is applied by hand with brushes; the dye spreads on the damp cloth to produce the color-shaded effect characteristic of yuzen. Yuzen is capable of achieving color effects of astonishing subtlety and complexity, and is used to produce the finest and most prized of all kimono fabrics.
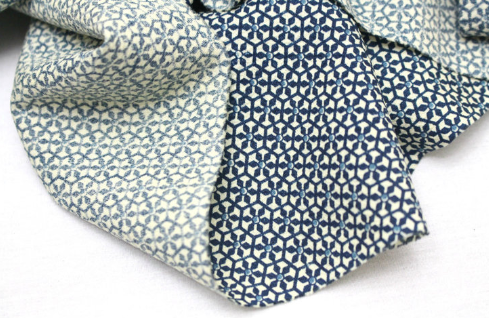
Kata Yuzen
A Kata is a hand cut stencil made of rice paper that was made waterproof by being smoked and coated in mulberry-juice. The stencil is used to apply rice paste to the fabric to repel dye from a part of the design. Each dye color is then hand brushed on. The registration of the stencils demands great precision. Fabric for Yuzen is generally very smooth so that the rice paste application can be done cleanly. Pigment is added by hand-painting using hake (brush), and dyes are usually only applied on one side of the fabric.
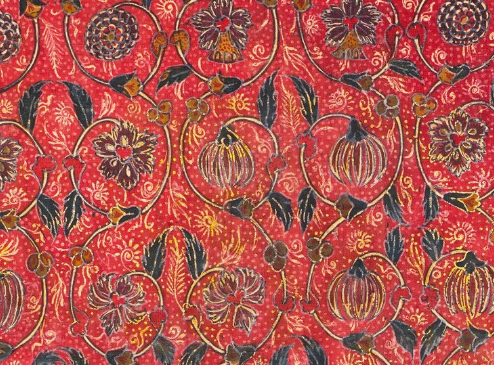
Sarasa
Edo-era sarasa is a tasteful and exotic dyed cotton cloth. The patterns on sarasa are of southern flowers, birds and people depicted in rich colors, and came to Japan from countries such as India, Java and Persia. Sarasa was introduced to Japan through the southern Nanban trade at the end of the Muromachi period, and had begun to spread by the mid-Edo period. Edo sarasa has a Japanese sensibility in its colors and designs and uses patterns created through stencil printing. These Japanese patterns are stylized and exotic. Usually, around 30 stencils are used but up to 300 stencils are sometimes used! When many stencil designs are layered together, the sarasa appear profound and almost three-dimensional. Edo sarasa is a beautiful craft preserved by craftsmen today who have inherited these traditional techniques from the Edo period.
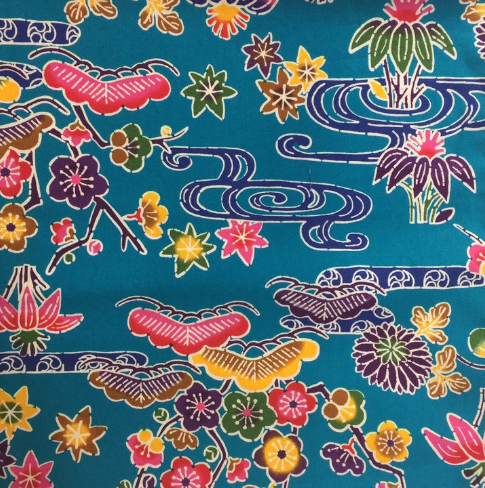
Bingata
The Okinawan art of bingata stencil dyeing can be thought of as a paste-resist version of batik. It uses multiple steps of stencil-applied paste and dyeing (either by vat dyeing or by hand application of dyes), with dyed areas covered with paste resist in subsequent stages of work. Bingata is typically produced in bright colors and with pictorial motifs of birds, flowers, and landscapes.
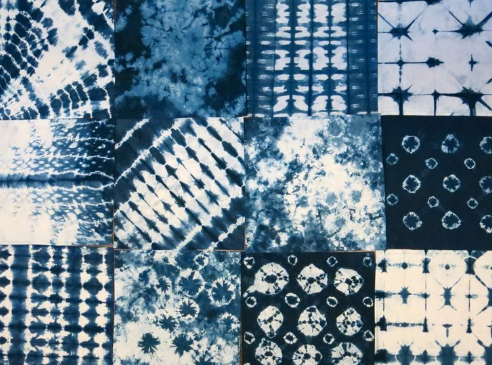
Shibori
Many shibori techniques exist and each creates distinctly different effects. What they all have in common is the use of tension on the fabric (by thread, clamping) , etc) to physically inhibit the spread of dye into areas of the fabric. Among the types of shibori dyed cloth at SuMoNo are: Katano (thread resist dots), Arashi (cylindrical wrapping and scrunching), Itajime (ee-tah-gee-meh - board clamping) and Nui (sewn pattern compression).
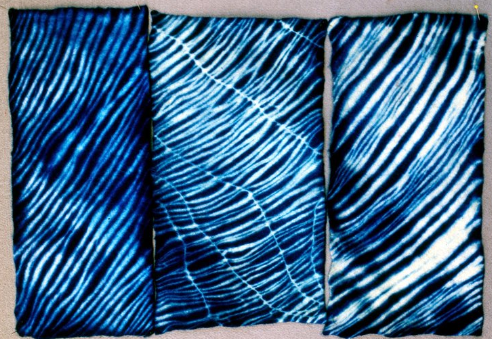
Arashi Shibori
Arashi shibori is also known as pole-wrapping shibori. The cloth is wrapped on a diagonal around a pole. Then the cloth is very tightly bound by wrapping thread up and down the pole. Next, the cloth is scrunched on the pole. The result is a pleated cloth with a design on a diagonal. "Arashi" is the Japanese word for storm. The patterns are always on a diagonal in arashi shibori which suggest the driving rain of a heavy storm.
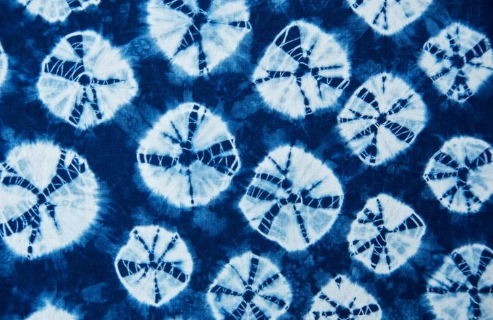
Kumo Shibori
Kumo Shibori is a pleated and bound resist. This technique involves pleating sections of the cloth very finely and evenly. Then the cloth is bound in very close sections. The result is a very specific spider-like design. This specific design requires very precise technique.
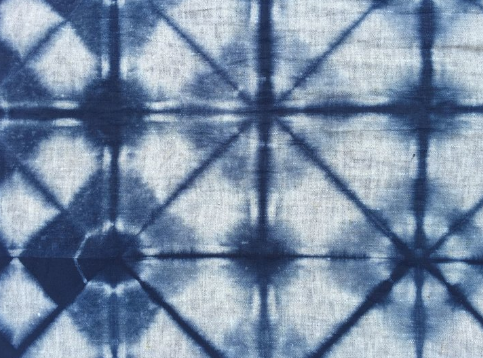
Itajime Shibori
Itajime Shibori is a shaped-resist technique. Traditionally, the cloth is folded and sandwiched between two pieces of wood, which are held in place with string. The bundle is then immersed in a dye bath. The shapes prevent the dye from penetrating the fabric they cover.
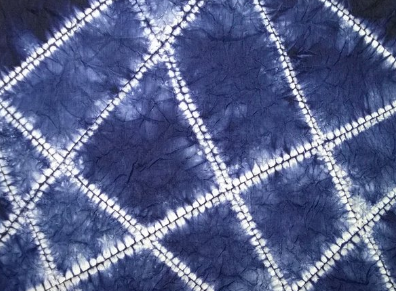
Mokume Shibori
A simple running stitch is used on the cloth then pulled tight to gather the cloth. The thread must be pulled very tight to work, and a wooden dowel must often be used to pull it tight enough. Each thread is secured by knotting before being dyed. This pattern is called Mokume, or “wood grain”.
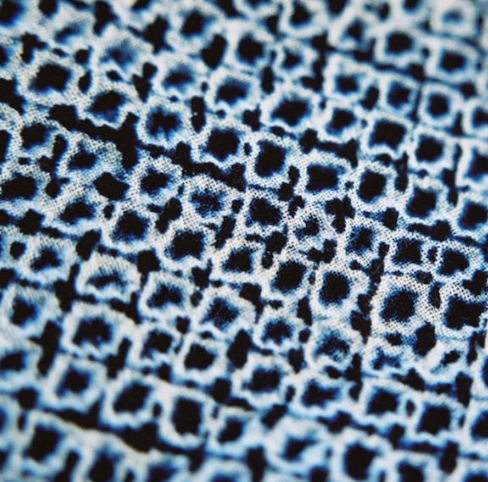
Miura Shibori
Miura Shibori is also known as looped binding. It involves taking a hooked needle and plucking sections of the cloth. Then a thread is looped around each section twice. The thread is not knotted; tension is the only thing that holds the sections in place. The resulting dyed cloth is a water-like design. Because no knot is used, miura shibori is very easy to bind and unbind. Therefore, this technique is very often used.
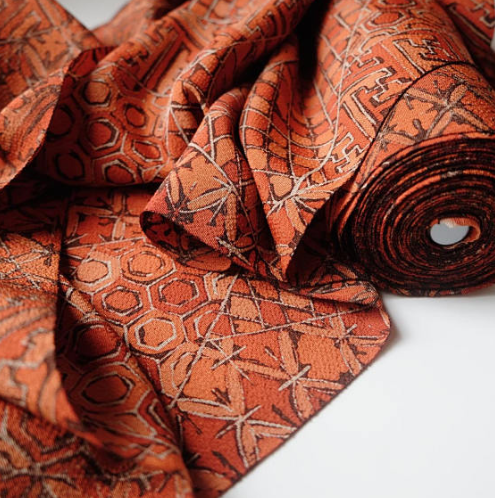
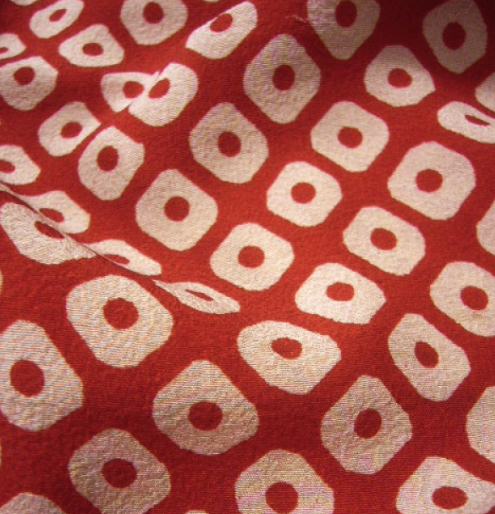
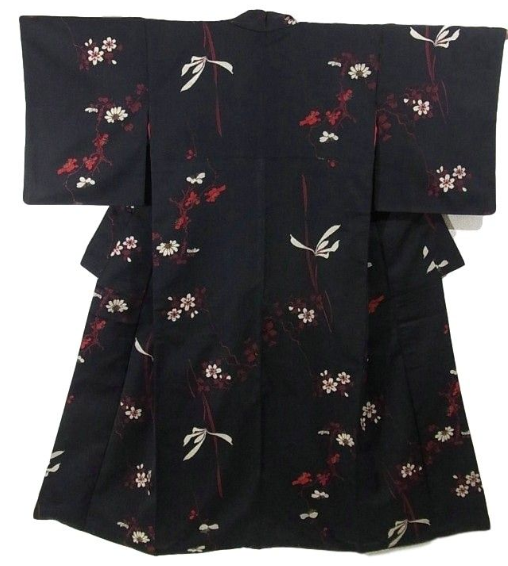
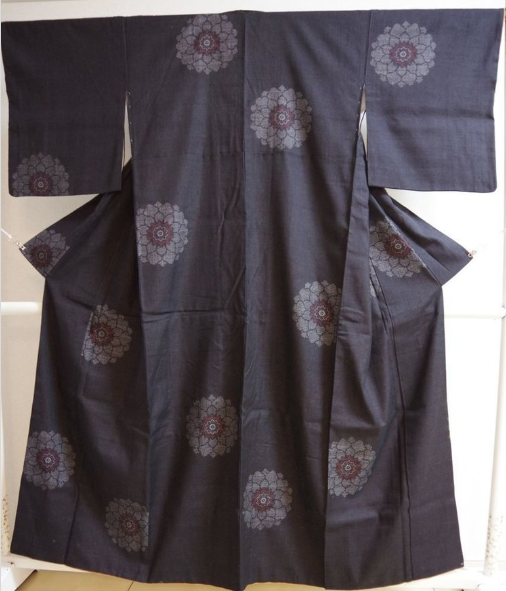
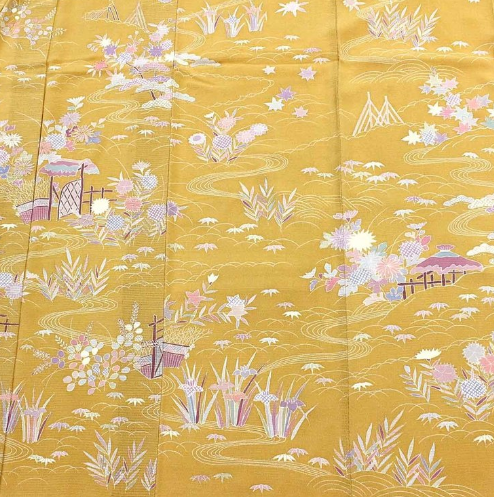
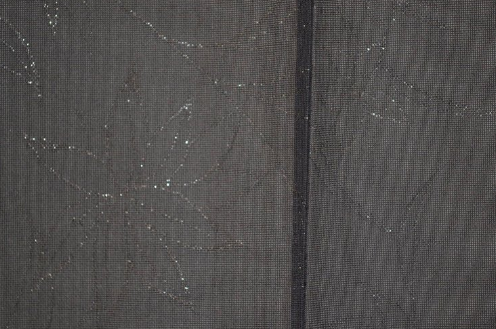
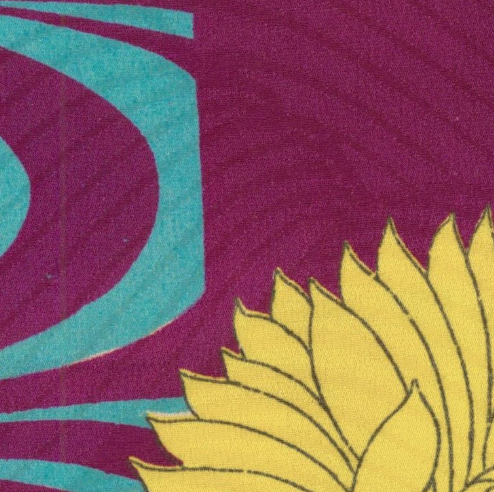
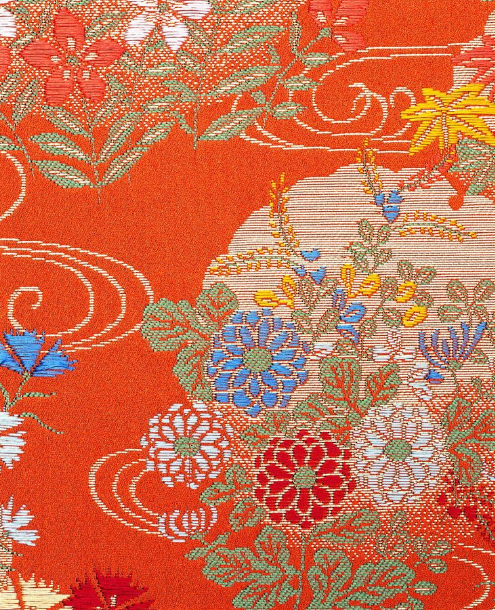
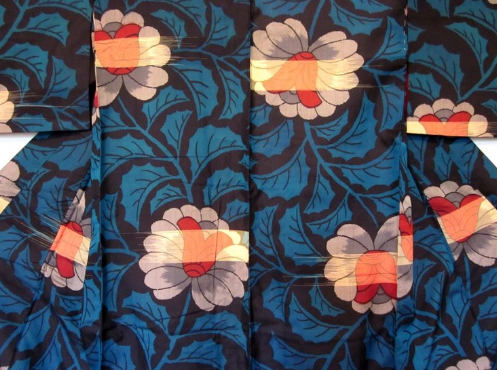
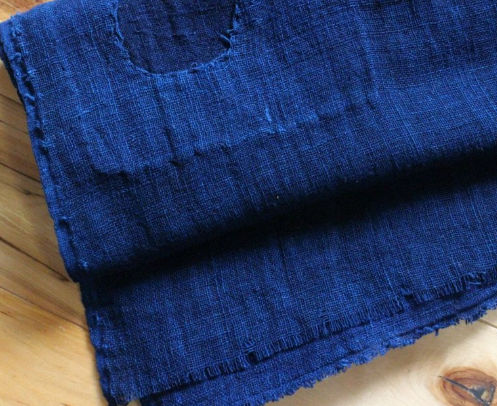
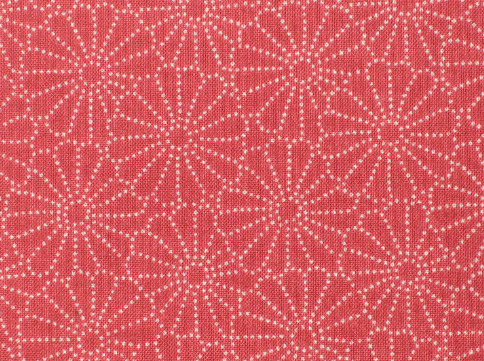
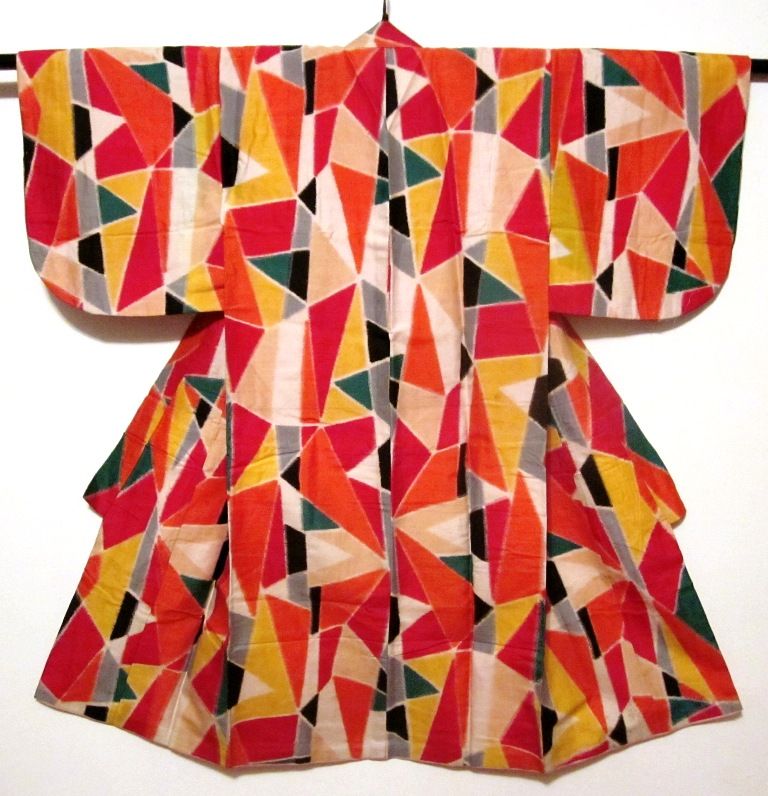
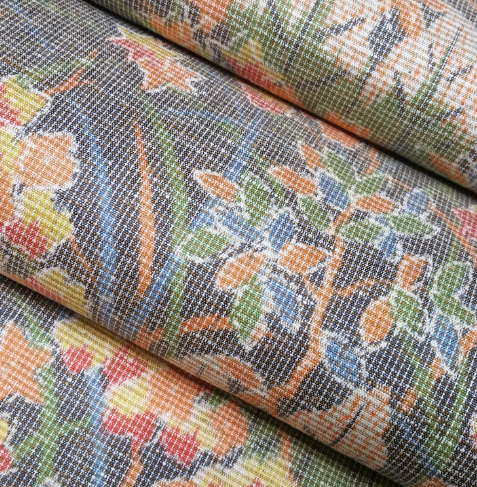
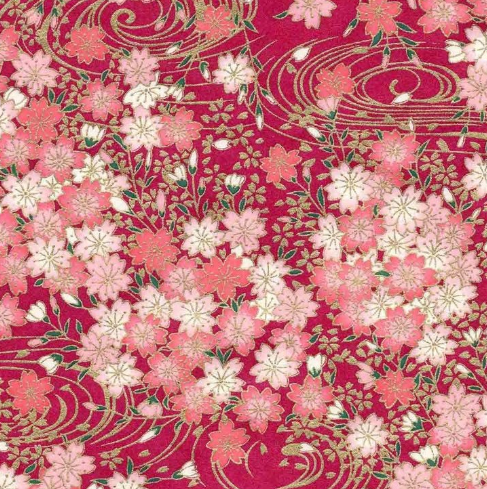
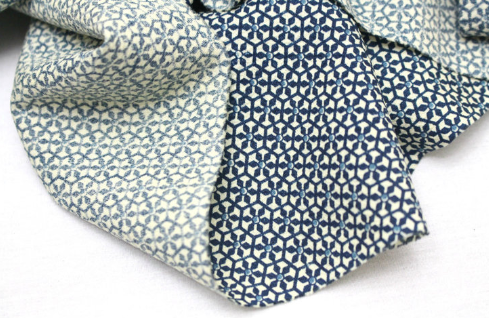
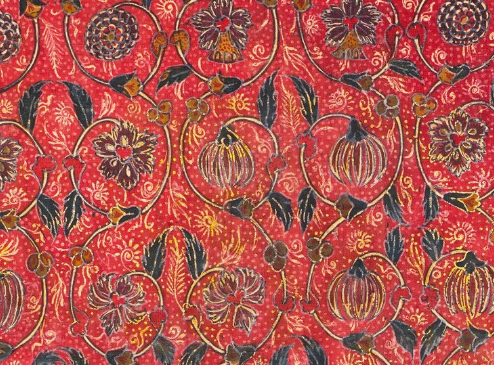
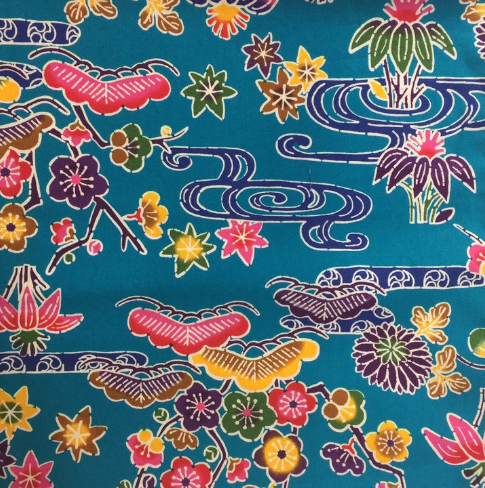
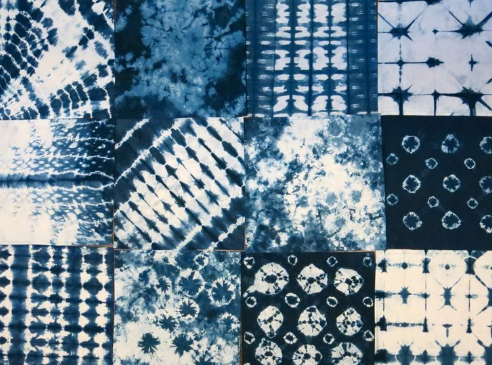
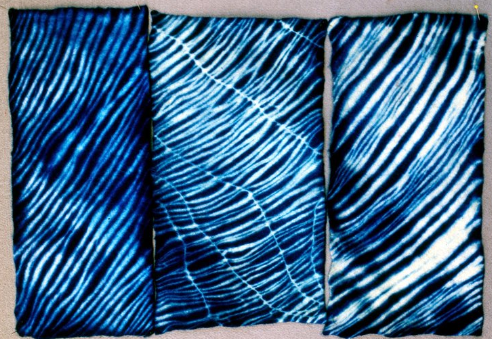
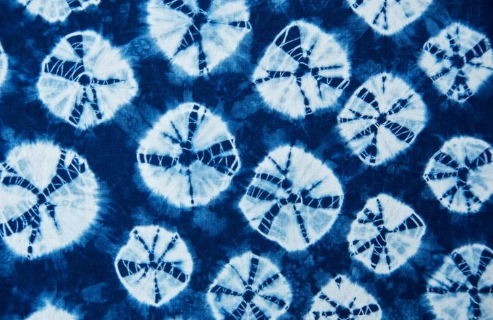
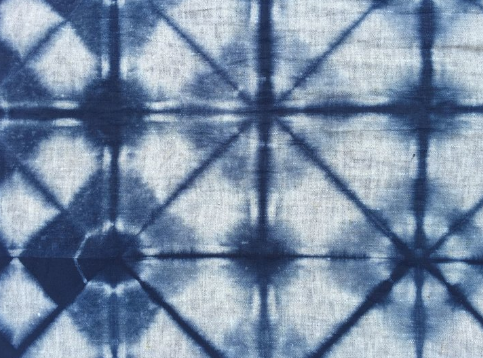
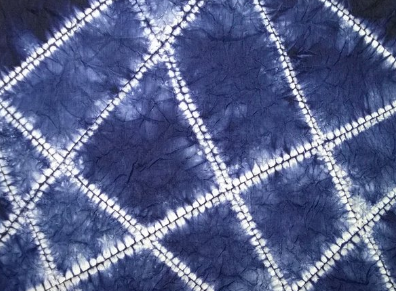
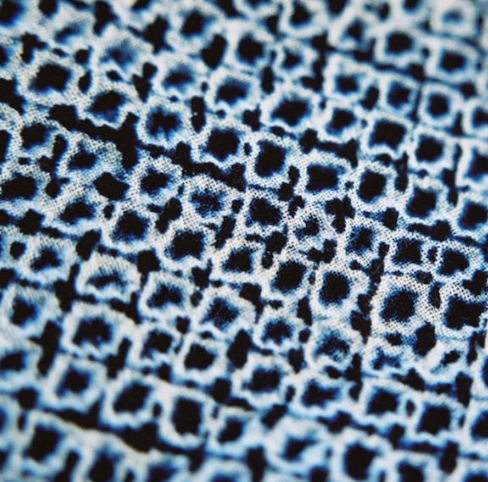