THE PROCESS
When a kimono is selected for re-interpretation as modern attire, it is unwrapped from its rice paper or acid-free transparent packaging, and immediately inspected for spots, tears or damage.
The vast majority of kimono come protected by traditional herbal treatments, used to eliminate insect damage during long storage in the semi-tropical climates in parts of Japan. At SuMoNo, we leave the herbal treatments in place until we are ready to work with the item, so they remain protected in their storage at our studio.
OUR SLIDESHOW WALKS YOU THROUGH IT…

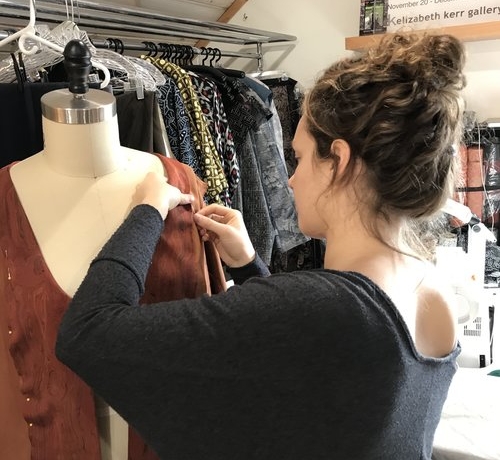
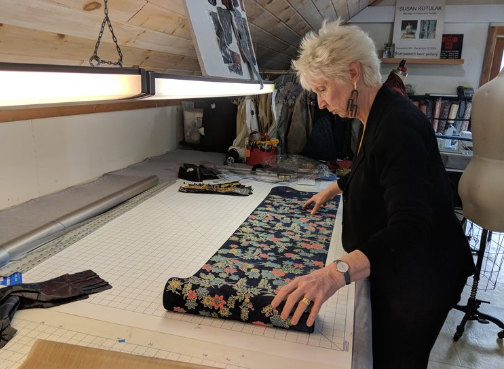
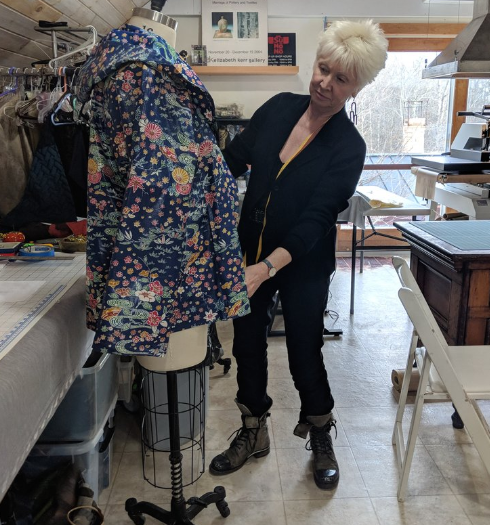
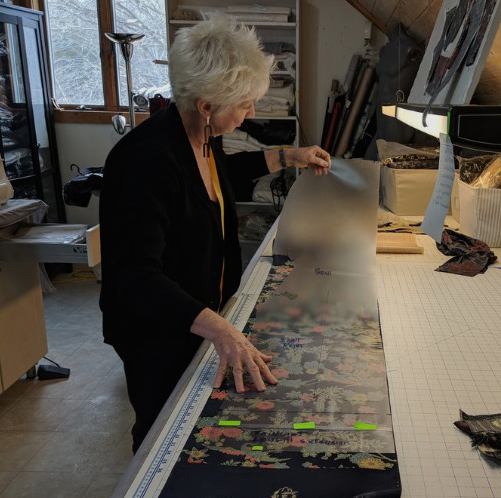

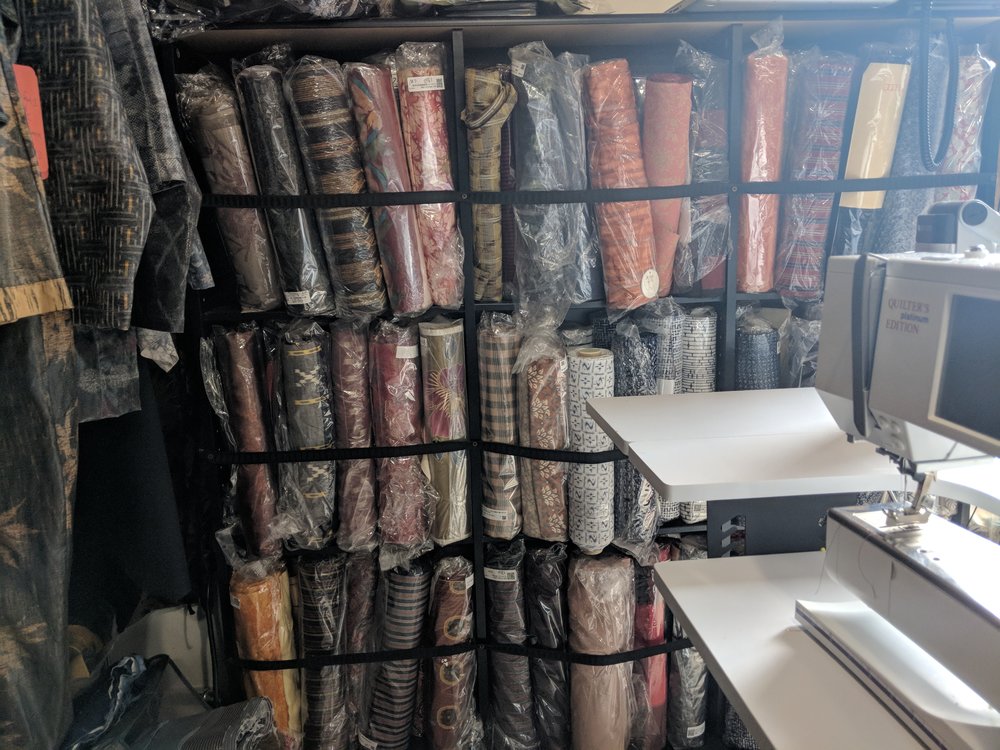
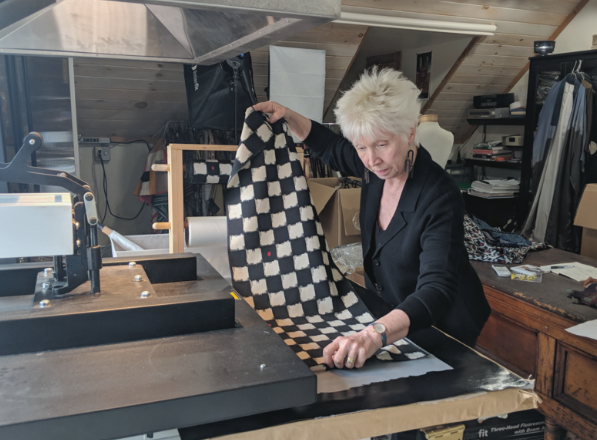

Once a kimono is selected, it is then treated in our in-house ozone chamber. Ozone chambers are a state-of-the-art technology for neutralizing any organic vapors and sterilizing the fabric. Ozone is even used for hospital linen, so it is extremely effective and safe for the fabric.
"I oversee all of the cutting. It sometimes requires several workings of the layout, before any cuts are made, in order to achieve satisfactory placement of the motifs in the finished garment. The large motifs that are the joy of traditional kimono are a very demanding aspect of this process. "- Susan Kotulak
For a kimono to work as a featherweight hooded raincoat, both sides of the fabric must be beautiful since the ‘wrong’ side shows, forming the striking lapels that drape toward the back hood. Only fabric done in Kasuri (Ikat) technique, jacquard weave or rice paste resist dyeing are suitable. The silk is inherently lightweight, and the laminating film is only 3mm thick, with no additional facings or linings, which makes for the lightest of all possible garments — ideal for travel, packing, and effortless wear.
Segments destined to become rainwear are re-inspected, ironed, de-linted, and carefully rolled up onto a hollow core to prepare it for laminating. This process takes at least an hour per garment, of very focused attention. Sewing for our rainwear is accomplished off-site, in small batches, using commercial machines that are required to handle the sewing of the laminate.
Each type of fabric responds differently to the laminate. The lightest, smoothest textiles take on a patent-leather-like quality, while the crêpe “chirimen” retain a matte or satin finish. In some cases, the colors are intensified by the laminating process — like wetting a beach pebble.
Each of our pieces is one-of-a-kind, and gives new life to a vintage garment that was designed, enjoyed, and preciously cared for in its earlier life. We delight in presenting these rejuvenated textiles in cuts to suit a contemporary lifestyle.